Employee Scheduling for Manufacturing:
Why Is Employee Scheduling for Manufacturing Important?
Central to a manufacturer’s operational success is its people: the dedicated production and warehouse staff, and the operations management teams who work tirelessly to support them. For these frontline contributors, the employee schedule serves as the central conduit connecting business operations to the people who get the work done.
Today’s operations managers rely on sophisticated technologies that produce vast amounts of data to help them plan and optimize production. But the same cannot be said for how those organizations plan, monitor, and optimize labor — an equally important aspect of operational excellence.
Because of the unique complexity of workforce management in manufacturing, the planning and scheduling of employees often relies on manual processes. Using hands-on approaches to create and communicate manufacturing work schedules, such as wrangling spreadsheets and updating breakroom boards, prevents manufacturers from realizing the powerful benefits of workforce scheduling optimization.
As the wave of digital transformation sweeps across the manufacturing landscape, automated and strategic employee scheduling is emerging as a linchpin. Scheduling software for manufacturing promises not just cost savings, but also heightened employee job satisfaction and a more agile, efficient operational framework. In fact, global organizations, including many Fortune 500 companies, have reduced labor costs and improved their overall operations through this approach.
In this guide, you will learn six best practices manufacturers are leveraging to increase productivity and reduce costs by optimizing their manufacturing shift schedules.
- Meet Production Targets with Improved Labor Forecasting
- Control Labor Costs with Responsive Scheduling Practices
- Disruption-Proof Operations with a Flexible Workforce
- Boost Retention with Worker-Centric Scheduling
- Ensure Safety with Adherence to Scheduling Rules
- Optimize Labor by Connecting Daily Operations to Workforce Capabilities
Best Practice 1: Meet Production Targets with Improved Labor Forecasting
Accurately planning and then assigning labor to meet production goals in the 60-120 days before the work gets done is a highly complex process to balance. The stakes are high to get it right: missing production goals due to understaffing may mean missing customer commitments, while incurring higher labor costs resulting from overstaffing can take a significant toll on the bottom line.
The reality is that constantly changing production requirements drive highly variable labor needs — and that’s difficult to predict with manual scheduling. For example, manufacturers who produce several products and are changing the production level mix frequently may have different staffing needs for each production line, each of which may require specialized skills or qualifications. Similarly, shifts in overall production levels may drive staffing changes not only within production, but downstream as well, in packaging or the warehouse.
Many manufacturers perform basic labor planning using manual tools such as Excel. While this approach is manageable at the outset, as the day-of work gets closer the velocity of change increases and the process breaks down. This is especially true when trying to predict labor needs and labor capacity at the department level, which is key to accurate labor planning. To improve the accuracy of mid-range labor planning, operations leaders need access to tools that can provide real-time data insights about the business (sales trends, weather predictions, seasonal production fluctuations, and more) and their workforce (employee pay rates, scheduling rules, availability, etc.).
Some manufacturers have data teams devoted to these analyses, while others use automated platforms to help. The important thing is to identify the most predictive leading indicators for the business so managers get a “big picture” view of upcoming labor resource needs compared to availability. Accurately aligning labor capacity to meet production goals—down to the department level—can be a game-changer for optimizing workforce operations.
How Technology Helps
Improving labor forecasting with labor management software that automates mid-term labor planning optimizes workforce operations, which frees up schedulers to navigate unforeseen, day-to-day scheduling fluctuations more effectively.
Best Practice 2 Control Labor Costs with
Responsive Scheduling Practices
Big opportunities exist for plant and operations managers to better control labor costs with improved employee scheduling strategies. Understanding the real underlying drivers of labor costs offers a smart starting point to reevaluate the employee scheduling workflow and associated scheduling policies. Here are three suggestions to consider as you examine cost control opportunities.
Don’t Throw Labor at the Problem
At a basic level, excessive labor costs could simply be a symptom of inaccurate mid-range labor planning as this impacts the short-term labor scheduling that happens several weeks before the work is performed. This is a critical time frame in the scheduling lifecycle because it’s when managers commit to a particular level of workforce capacity and publish work schedules accordingly.
Not having the necessary staff needed to meet production goals during a given point in time, and then “throwing labor at it,” is a costly strategy. Better mid-range labor planning is essential for labor cost control. With improved accuracy, managers can avoid costly overtime by fine-tuning the labor plan to support last-minute requirements using day-of scheduling strategies such as flex pools or cost-effective temp resources.
After improving their workforce scheduling practice, a “Big 3” automaker with over 100,000 employees in North America saved $800 per employee per year on grievances associated with wrongful overtime assignments.
Optimize the Schedule for Cost
Understanding the cost implications related to manufacturing shift schedules can help control labor costs. Use workforce data to respond strategically to operational changes such as sudden spikes in demand or unexpected worker callouts. By having visibility into information about workers’ base pay rates, overtime status, recent work history, or other pay rate triggers, managers can schedule the most cost effective, qualified workers for each role.
Leveraging labor cost insights during the scheduling process is an excellent way to reduce wasteful overtime, avoid overstaffing, and create an optimized schedule.
Plan for the Unexpected in the Short-Term
A high incidence of short-notice worker callouts during the pandemic amplified the need for more strategic scheduling practices. One cost-effective strategy for responding to last-minute worker callouts is to build a flexible, responsive workforce. Flexible work schedules in manufacturing, which we cover in detail in the next section, help facility managers control labor costs in the face of unexpected change by giving them the information needed to assign and communicate with the most cost-effective workers — quickly filling those open shifts.
With real-time data insights and the right automated processes in place, schedulers can tap hidden workforce capacity to quickly backfill shifts while taking into account other critical factors like compliance, employee certifications, and potential overtime costs.
Scenario planning for unexpected events, such as staff shortages or equipment breakdowns, is essential for maintaining operational resilience. Manufacturing facilities should develop contingency plans that identify critical roles and the skills required for those roles, ensuring that alternative staff can step in seamlessly when needed. This might involve cross-training employees so they can perform multiple functions within the plant or having a pool of temporary workers who can be called upon during peak periods or emergencies. By proactively preparing for various scenarios, manufacturers can minimize disruptions and maintain productivity even when unforeseen issues arise.
According to an Aberdeen study, 42% of organizations utilizing automated scheduling tools also implemented scenario planning software to more accurately align their labor expenses with real-time service demands. By predicting labor requirements based on historical data, manufacturers can strategically synchronize labor scheduling with business operations, yielding significant bottom-line benefits. This practice not only optimizes labor costs but also ensures that staffing levels meet actual service needs, enhancing overall efficiency and productivity.
How Technology Helps
In much the same way as plant managers use sophisticated ERP technologies and data to plan production, employee scheduling software exists to enable data- driven decision-making for workforce operations. This results in more accurate labor planning, efficient labor utilization, and daily operational resilience—critical factors in keeping labor costs under control.
Customers reported a 21 percent decrease in overall labor costs.
2021 Shiftboard Customer ROI Survey
Get manufacturing insights delivered right to your inbox. Subscribe now.
Best Practice 3: Disruption-Proof Operations
with a Flexible Workforce
A top goal for operations managers is to ensure all critical job openings are filled — manufacturers simply can’t run production lines or fill orders without the necessary people to do the work required. This challenge can be very stressful for schedulers to navigate, especially during times of peak demand.
Building flexibility into your employee scheduling workflow is key to avoiding operational disruptions. Here are three flexible scheduling strategies manufacturers use to keep the frontlines running.
How Technology Helps
Employee scheduling software can automate selection processes such as employee skill sets and overtime status and creates a streamlined approvals process for employee leave requests. The right solution helps organizations meet operational needs while providing their workers with greater control and flexibility over their work schedules.
Leverage Flex Pools
Flex pools are a useful strategy to leverage when unplanned events impact production volume and labor demand. The structure of flex pools varies by plant and facility — some companies create flex pools organized by role, production line, or department. Others create flex pools to address a particular challenge, such as workers who are eager to volunteer for overtime. The common attributes of flex pool employees are that they possess versatile skill sets and have flexibility in their work schedules.
Some manufacturers staff their flex pools in-house, leveraging part-time workers or full-time employees, while others include contingent labor sources. Regardless of the labor source, real-time visibility into workers’ qualifications, overtime status, and availability is essential to this strategy’s success.
Customers reported an 88 percent improvement in shift coverage rate.
2021 Shiftboard Customer ROI Survey
Offer Self-Serve Scheduling
Production facilities typically create manufacturing shift schedules using a top-down approach, with work schedules set far in advance. However, other scheduling strategies can be used for short-range scheduling. For example, adding in bottom-up scheduling (self-serve scheduling where workers pick up the shifts they want to work) is a complementary strategy used in tandem with traditional top-down scheduling to fill coverage gaps with qualified, eligible, and willing workers.
Self-serve scheduling strategies also have the added benefit of improving job satisfaction because they provide workers with the ability to pick up or sign up for open shifts themselves, giving them more autonomy over their work-life balance. Findings from Shiftboard’s 2023 Hourly Worker Research Report revealed that 78% of hourly workers want more autonomy to select shifts versus being assigned to them, and 76% want the ability to trade shifts once they are assigned. Additionally, 81% said they prefer having mobile access to their work schedules. Self-serve scheduling capabilities relieve supervisors of time-consuming administrative duties, empower employees with more control, and improve operational efficiency.
Adjust Shift Patterns and Durations
Shiftboard has helped our employees get more visibility into their work schedules and make changes on the go. It is easy to use and has provided more structure to our scheduling process.
Tyler Blake
Senior HR Generalist, Daisy Brand
Plant operators can create more flexibility by changing how they structure shifts. For example, one of the largest chicken processing plants in the United States created alternate shifts (shifts cut into shorter periods). This change expanded their workforce, as it attracted more workers who were looking for adaptable schedules. The plant was able to structure mini-shifts to accommodate these new workers and keep operations running smoothly.
Other strategies include adjusting shift start, stop, and break times to coordinate with workers’ personal demands, such as transporting children to and from childcare, home, or school. Adjusting shift lengths, patterns, and break times provides employees greater flexibility to manage work with life — and does so without interfering with plant productivity.
Best Practice 4:Boost Retention with
Worker-Centric Scheduling
Most organizations understand work schedules play a role in employee productivity and turnover, yet they underestimate the extent to which schedules impact employee job satisfaction. More importantly, most employers aren’t aware of their potential to create work schedules capable of meeting individual employee needs.
Work schedules heavily influence employee satisfaction and retention because they impact life more acutely than any other aspect of work: earning potential, parenting schedules, social lives, and quality of life, just to name a few. In other words, the work schedule has a huge impact on how people manage their time — a key component of work-life balance.
In fact, according to Shiftboard’s research, 75% of the hourly workers polled ranked work-life balance as necessary for high job satisfaction. This is rather surprising when you consider work-life balance ranked even higher than having a good working relationship with a boss (64%), working in a convenient location (63%), comprehensive benefits (58%), or doing enjoyable tasks or projects (55%). The findings strongly suggest the key to hourly employee job satisfaction is tied to the degree that workers feel empowered to balance work with life.
These findings uncovered the need and opportunity that exists to change the way work is scheduled. The task is especially acute in the manufacturing industry where highly skilled labor is employed — and the replacement cost tied to turnover is high. Here are two strategies you can use to improve job satisfaction and retention at your facility.
Empower Workers to Influence Their Schedules
The manufacturing work schedule is a critical lynchpin for smooth operations, as well as interpersonal relationships. Of the hourly workers surveyed for Shiftboard’s study, 82% reported that their work schedule impacts their overall job satisfaction. Further, 71% said their schedule impacted their relationships with co-workers, and 79% stated their work schedules influenced their likelihood of seeking other employment opportunities.
Worker-centric scheduling considers worker preferences and empowers employees with more autonomy over their work schedule. Allowing workers to communicate their availability, self-schedule, trade shifts, or volunteer for overtime can dramatically improve their perceptions about job satisfaction and reduce turnover.
In Shiftboard’s study, 78% of hourly employees wanted the ability to select their shifts rather than having them assigned at random, and 76% found it important to be able to swap shifts once the schedule was posted.
This can be a win-win for both employees and employers, as labor scheduling affects more than just job satisfaction. When surveyed, Shiftboard customers reported an average 55% improvement in employee productivity. The research is clear: work schedules can directly impact top-line revenue and bottom-line profits.
Customers reported an 86 percent improvement in employee satisfaction and a 55% improvement in employee productivity.
2021 Shiftboard Customer ROI Survey
Test Self-Serve Scheduling
In response to these drivers of job satisfaction, some manufacturers have had great success with innovative, self-serve strategies such as voluntary overtime. When one medical supply manufacturer implemented an all-volunteer overtime policy (where employees just signed up if they wanted overtime) the results were astounding. The company was able to increase the fill rate of overtime shifts to almost 100 percent every single week. This is an excellent example of a win-win — the company got overtime filled, and the employees who wanted to work extra got the overtime hours.
How Technology Helps
Employee scheduling solutions fill shifts with qualified staff while prioritizing worker preferences and enabling bottom-up scheduling. This results in organizations attracting and retaining the skilled labor that is instrumental to success in the manufacturing industry.
Another benefit of these kinds of self-serve strategies is transparency. When transparency is built into the scheduling process, workers understand how shift assignments are made and trust the scheduling process. Without transparency, employees are left to make dangerous assumptions. In fact, 45% of the hourly workers surveyed said they would leave an employer due to perceived scheduling unfairness. While it is almost impossible to make everyone happy with a work schedule, involving employees in the process and ensuring they understand the rationale behind scheduling decisions will take out the guesswork and significantly improve retention efforts.
According to Shiftboard’s study, 90 percent of hourly workers are willing to work overtime as long as it’s optional.
Shiftboard’s 2023 Hourly Worker Research Report
Best Practice 5:Ensure Safety with
Adherence to Scheduling Rules
Production lines and warehouses are inherently dangerous work environments. Every time a worker steps on the floor, their health, safety, and well-being are on the line. It’s not just the physical conditions that put them at risk: a chaotic, overly taxing pace and employee scheduling issues also play a role. But they often go unrecognized amid the challenges of hitting quotas and keeping customers satisfied.
Staying compliant with dozens of labor regulations, from the federal level to union agreements and local labor laws, is a complex process to manage. In 2024 and beyond, that task becomes even more challenging, as managers must stay on top of changing laws, regulations, and agreements.
A huge benefit of using Shiftboard’s software is being able to identify potential grievance situations before assigning shifts to our employees. One of the built-in reports can analyze our entire schedule, allowing us to re-arrange the shifts before finalizing and distributing it to our employees. The ability to systematically check for compliance has been the main factor in reducing the number of union grievances.
Plant Manager
“Big 3” Automaker
Although time-consuming when managed manually, having processes in place to continually check your employee schedule against all established rules requirements (especially during critical moments such as day-of backfilling) helps to ensure a fully compliant schedule is maintained, and that workers are safe. Having access to real-time data insights can also help managers understand the tradeoffs between shift coverage needs and compliance requirements so that scheduling decisions can be justified with confidence.
Manufacturers spend millions annually to ensure a safe working environment for their frontline workers. Yet aligning employee scheduling strategies with their safety initiatives is often overlooked. Relying on manual employee scheduling methods, like spreadsheets, can lead to unintended errors that compromise safety and potentially violate safety regulations and policies, such as:
- Assigning tasks to workers who don’t have required credentials or training.
- Allocating back-to-back shifts without adequate rest periods.
- Scheduling workers for OT assignments that may significantly increase fatigue.
- Inexperienced schedulers or managers inadvertently breaking essential scheduling rules.
By implementing oversight through employee scheduling automation, manufacturers can ensure a safer workplace. Intelligent scheduling technology guarantees adherence to essential guidelines, automating rules compliance from schedule creation to execution. This proactive approach ensures only qualified and eligible workers are assigned to shifts, mitigating risks like breaches of rules, CBA agreements, fatigue regulations, and other labor laws. Furthermore, this automation provides clear visibility into credentials and training, helping to prevent the costly disruptions that arise when unqualified workers are inadvertently scheduled.
How Technology Helps
Intelligent employee scheduling technology can ensure a safe workplace by automating rules compliance during schedule creation and throughout the scheduling lifecycle, ensuring only qualified, eligible workers are assigned to shifts.
Integrating Fatigue Management into Scheduling
Fatigue management is crucial for ensuring both safety and productivity in manufacturing environments. Staff scheduling that considers fatigue levels can prevent accidents and improve overall efficiency. Incorporating regular breaks and rotating high-intensity tasks among workers can help manage fatigue effectively. These practices ensure that employees remain alert and perform their duties safely and efficiently.
Rotating high-intensity tasks can distribute the workload more evenly and prevent overburdening specific employees. This not only reduces fatigue but also enhances job satisfaction and productivity. With real-time data and employee scheduling software, manufacturers can monitor employee fatigue levels and make necessary adjustments to the schedule. By prioritizing fatigue management, managers can create a safer and more productive work environment, ultimately leading to better operational outcomes.
Best Practice 6:Optimize Labor by Connecting Daily
Operations to Workforce Capabilities
Employees perform much better in shifts and roles that they are qualified for or that they select themselves. That’s why managers need a process for understanding and tracking how various worker attributes factor into productivity and scheduling decisions — across all labor pool resources (full-time, part-time, contract labor, etc.).
To develop successful strategies to retain employees and maximize productivity, employers first must understand their hourly worker needs, while also recognizing these needs will vary.
Rick Webb
Director, Grit Studios
One strategy for gaining a holistic view of labor resources is to create and maintain a central database with detailed employee profiles. Armed with insights into individual worker attributes such as work preferences, overtime status, schedule flexibility, credentials, and productivity by role, among others, managers can schedule workers strategically to drive higher productivity and avoid unnecessary overtime.
Skill-based Scheduling
Skill-based scheduling is a strategic approach that leverages the specific skill sets of employees to optimize scheduling and ensure that the right people are assigned to tasks requiring particular expertise. By maintaining a detailed record of each employee’s skills, certifications, and qualifications, managers can create employee schedules that match workers to roles where they can be most effective.
This ensures that critical tasks are completed by the most qualified individuals, reducing errors and increasing efficiency.
Implementing skill-based scheduling involves regularly updating employee profiles to reflect new skills acquired through training and experience. Managers can use this data to identify skill gaps and provide targeted training programs to address them, further enhancing workforce capabilities. Additionally, skill-based scheduling can improve employee satisfaction by aligning work assignments with employees’ strengths and goals, fostering a more engaged and motivated workforce.
Connecting daily operations with the labor resources available is a complex and ever-changing aspect of manufacturing. With data-driven decision making and real-time communication tools, managers can achieve higher workforce capacity and efficient labor utilization while ensuring workers’ needs and preferences are considered throughout the scheduling lifecycle.
Customers reported a 31 percent improvement in employee callouts and 16 percent less turnover.
2021 Shiftboard Customer ROI Survey
Enterprise companies have complex employee scheduling needs and require solutions that are both highly configurable and easy to use.
Frank Pereira
Managing Partner
Coleman Consulting Group
Organizations can put themselves in the driver’s seat when solving the enduring human capital problem of managing and scheduling their workforce. With tailored employee scheduling software for manufacturing, operations leaders can effectively scale operations while keeping an eye on bottom-line profits and employees’ well-being.
Employee scheduling technology automates the scheduling lifecycle using data-driven tools designed to create optimized employee schedules each and every day. From accurate labor forecasting to assigning the best workers to managing change efficiently and ensuring labor compliance, intelligent, automated technology is key to realizing the powerful benefits of workforce scheduling optimization.
Customers reported 30 percent faster schedule creation and 28 percent less time wrangling schedules throughout the scheduling lifecycle.
2021 Shiftboard Customer ROI Survey
Take the Best Practices Guide with you.
In this eBook, you will learn six best practices manufacturers are leveraging to increase productivity and reduce costs with better staff scheduling strategies.
Trusted by the World’s Most Recognized Brands
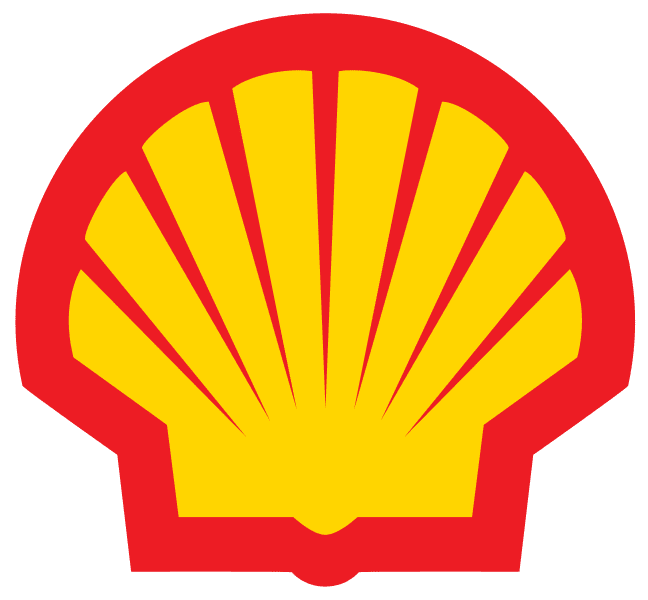
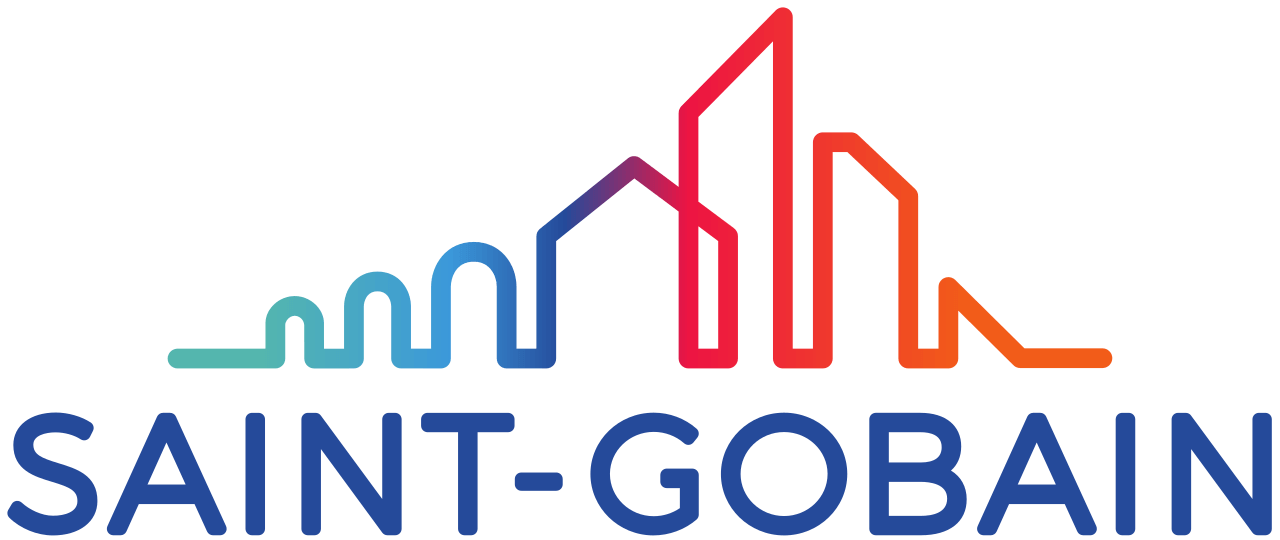
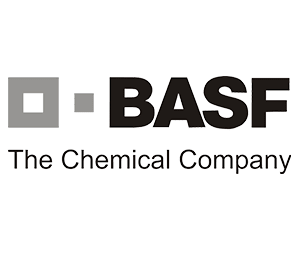